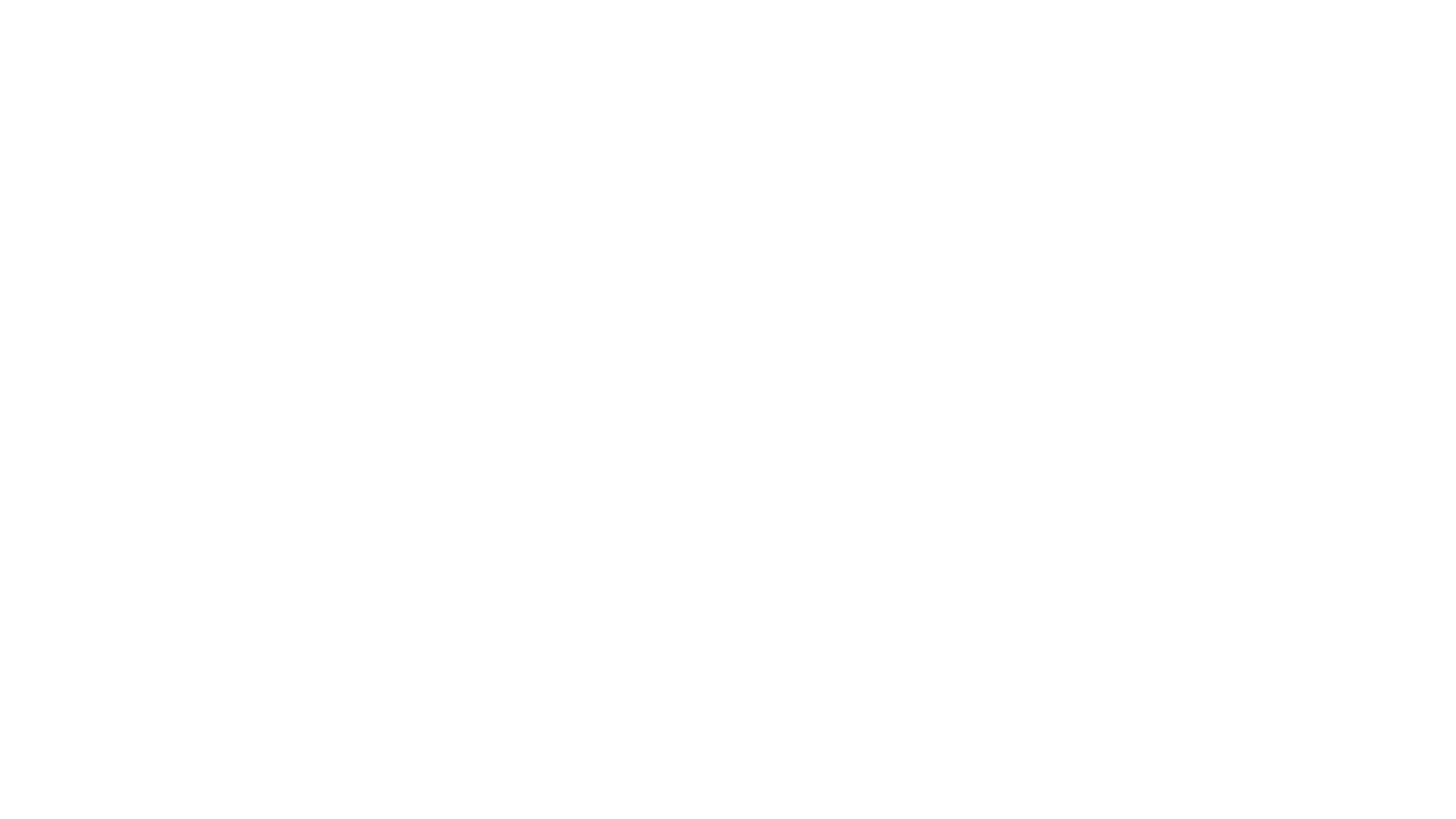
Does low-price wind harm safety and efficiency?
On Monday, professional services firm ARMSA Consulting published a report called ‘The Great Leap Forward’, which it produced in conjunction with our colleagues at A Word About Wind’s parent firm Tamarindo Group.
Global wind capacity trebled to 651GW in the last decade driven by growing turbines and falling costs. But is this stronger commercial case at the cost of projects’ safety and efficiency? That’s a question discussed in a new report.
On Monday, professional services firm ARMSA Consulting published a report called ‘The Great Leap Forward’, which it produced in conjunction with our colleagues at A Word About Wind’s parent firm Tamarindo Group.
The report features interviews with experts from wind giants including MHI Vestas, Siemens Gamesa and Vattenfall.
It looks at the impact of growth in wind on how projects are developed, built and operated; and raises concerns about how firms invest in employee skills. In particular, it focuses on how to improve the ways that employees throughout the project life cycle are trained to make the right decisions. It also discusses the negative financial impacts of current training on profits.
Four pillars
Budget, quality, safety and time. These are the four pillars used to determine whether a project is successful, but they must all be kept in balance. Getting people to focus too much on one tends to come at the expense of others.
The report says focusing too much on budget could come at the expense of safety and mean people miss chances to optimise projects.
Let’s look at offshore wind. Strike prices in the UK’s Contracts for Difference regime have plummeted in recent years. Last September, the government gave support for projects at a record low of £39.65/MWh, which is around a third of the level it was in 2017.
The impact of these falling costs is that developers have to focus on driving down the cost of projects to ensure they stay profitable. Interviewees in the report say that this focus on cost was squeezing budgets of firms throughout project value chain. This is reducing the amount of money that companies have to invest in training employees.
In addition, the report says firms are looking at automation and digitalisation to make projects more efficient. That is understandable and we certainly see the major benefits of technology like predictive maintenance. But it argues that firms aren't making similar investments in optimising the skills of their people.
When they do, it says firms invest too much in dated classroom-based training where it is almost impossible for employees to recall everything they’ve been taught when they actually need it.
This impacts on the decisions they make – from technicians to office-based staff – and thus the safety and efficiency of wind developments.
Going with the flow
The report offers an alternative: workflow learning.
This is a form of continuous learning where employees could use an online platform to support them to improve their decisions while they’re actually working – ‘in the workflow’ to use the jargon.
For example, with a virtual platform, a technician wouldn’t need to remember what they were taught in a classroom long ago, or travel across the country to get the manual. They could be trained remotely from a phone or laptop.
It says this could help with improving operations and maintenance practises in what is still a young sector. Wind does not have the same years of experience as the fossil fuel industry does to manage projects safely.
The risks are different too, of course. Wind turbines cannot spill millions of barrels of air into the sky. And one failure rarely knocks out a whole project.
However, if developers don’t give their workforce the right training, mistakes are likely to be made. At worst this would mean injuries or death and could cost a developer millions of pounds in damages, lost production and legal fees.
Failing to optimise decision-making also results in many small losses over the years, adding up to a big impact on the bottom line. Conversely, investing in improving worker skills in the workflow could help to improve results.
We’re sure this would be welcomed by investors. Improving a workforce’s skills to prevent safety hazards can boost productivity and return on investment. This can't be forgotten as companies race for growth in the 2020s.