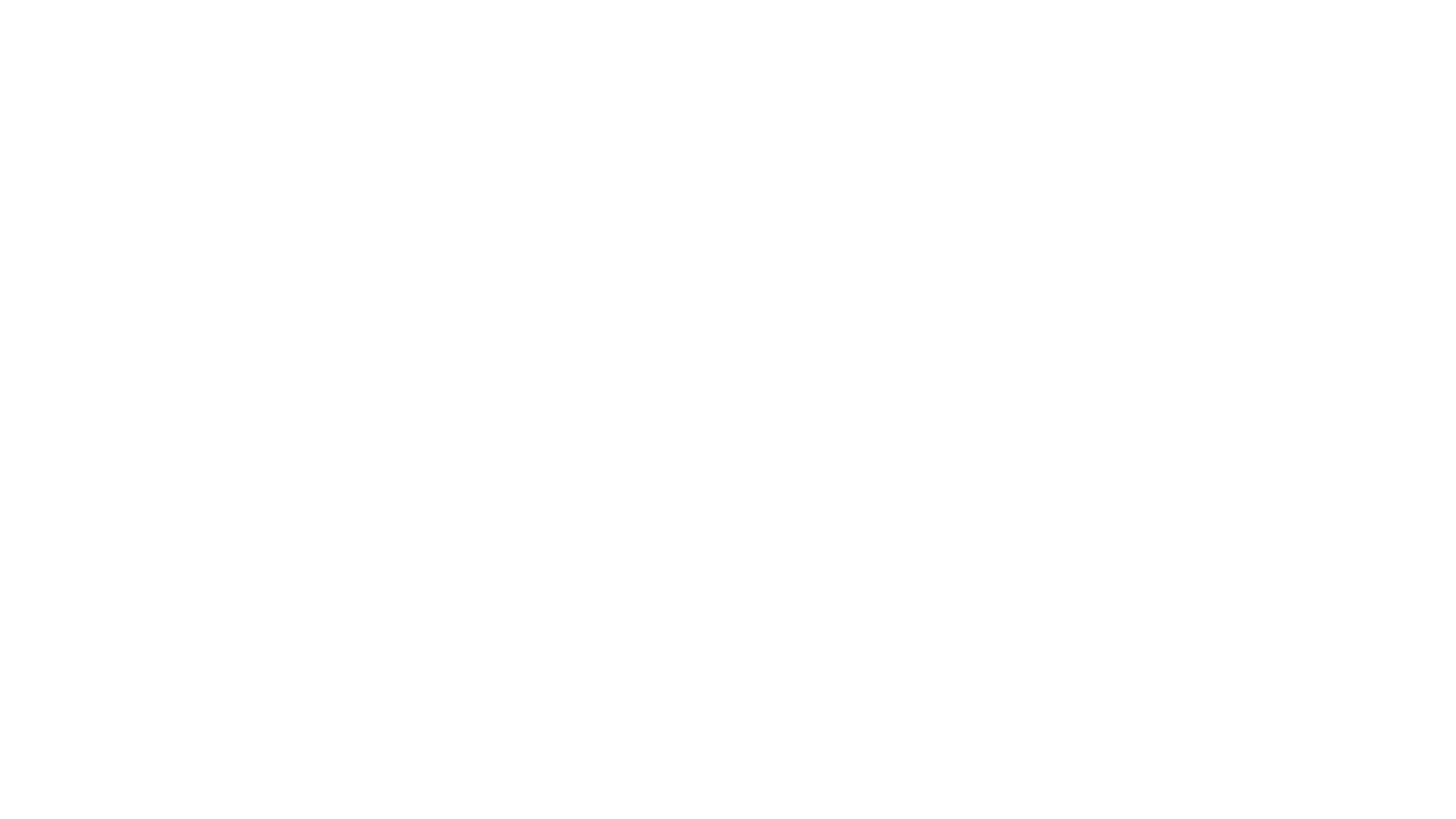
Extending turbine life: ONYX InSight's John Coultate on oil condition monitoring
We are set to host our inaugural European Wind Investment Awards on 31st October. Before the event, we're looking at the companies shortlisted in our Innovation Award category, and how they could influence the industry.
In this edition, we speak with John Coultate, Head of Product Development at predictive maintenance analytics firm ONYX InSight to talk about its joint project with industrial and automotive lubricants global brand Castrol, to better understand how companies monitor the condition of oil in turbines.
What is oil analysis?
ONYX InSight and Castrol have been working to complete the first independent study on oil sensing for the wind industry. Their goal is to understand how companies analyse the condition of the oil in their turbines, in order to help improve processes, extend the lives of turbines and, ultimately, to boost financial returns.
Oil condition monitoring is currently a laborious process for wind turbine operators, subject to delays and errors: poor sampling methods mean oil samples may not be representative and analysis inaccurate; long waits for test results contribute to turbine downtime and cost money; and sub-optimal responses driven by poor data lead to increased lifetime maintenance costs.
“Oil analysis data usually comes from a lab. Normally what happens is that a technician climbs a turbine, take a sample of oil, which then gets sent off to a lab every six or 12 months”, Coultate told us.
However, this data is difficult to combine with any other information on the wind turbine, with the resulting data being inconsistent, and depending very much on how the technician has sampled the oil. “The sampling process is also quite infrequent, so it’s very difficult to trend the oil and its properties."
ONYX and Castrol have been testing different oil sensors in the market with the aim to combine oil sensor data with vibration condition monitoring and wind turbine operational data in a single software platform. This would enable companies to have a better understanding of oil condition and, by combining it with other health indicators, be able to improve the performance of their maintenance and repair teams, increasing profitability.
The project consists of two phases. Phase one was laboratory testing: “For this first phase we had seven different types of sensors and four different types of oil tested in a laboratory. This helped understand what these sensors could and couldn’t detect. And it also helped understanding which sensors worked well for wind turbine applications,” Coultate said.
This has led to phase two of the project, which involves installing sensors on wind turbines: “We are in the middle of phase two now, and we are installing five different types of sensors on ten wind turbines in North America.”
This dataset is going to help ONYX and Castrol to understand how these sensors work in a laboratory environment and in the real world environment. The results will be then presented at conferences and webinars, and shared with the industry.
Why is this an innovation?
Oil condition monitoring analysis is just one piece of the puzzle.
ONYX and Castrol aim to combine that information with other maintenance information, including vibration monitoring, to expand wind operators’ ability to monitor the health and condition of wind turbines.
“Those turbines already have our hardware for vibration monitoring and we are using the same hardware to acquire data from oil sensors”, Coultate said. “Vibration condition monitoring is well adopted now in wind and it’s extremely good for detecting gearbox and drivetrain faults.”
However, the combination of these data would be very valuable in predicting future problems in the machine and enhancing the turbine’s performance.
Why is it in our shortlist?
Combining vibration and oil sensing is set to help companies gain a complete picture of the health of their turbines, and bringing together all these different kind of data in a software platform should help operators make more informed decisions on maintenance.
The aim is to improve condition monitoring in the wind sector by providing cost-effective fault detection solutions. This would enable wind companies to reduce maintenance costs by thousands of pounds per annum, per turbine, ONYX and Castrol have estimated. These potential savings caught the eye of our judges.
We will be revealing the winners of the 13 categories in our European Wind Investment Awards at a ceremony in London on 31st October.
On the same day, we will look at the biggest issues facing wind investors at our Financing Wind Europe conference. To register to attend, you can check out our Financing Wind Europe site. If you've reached your quota and would like to buy more tickets, please contact Zoe on zoe@awordaboutwind.com.