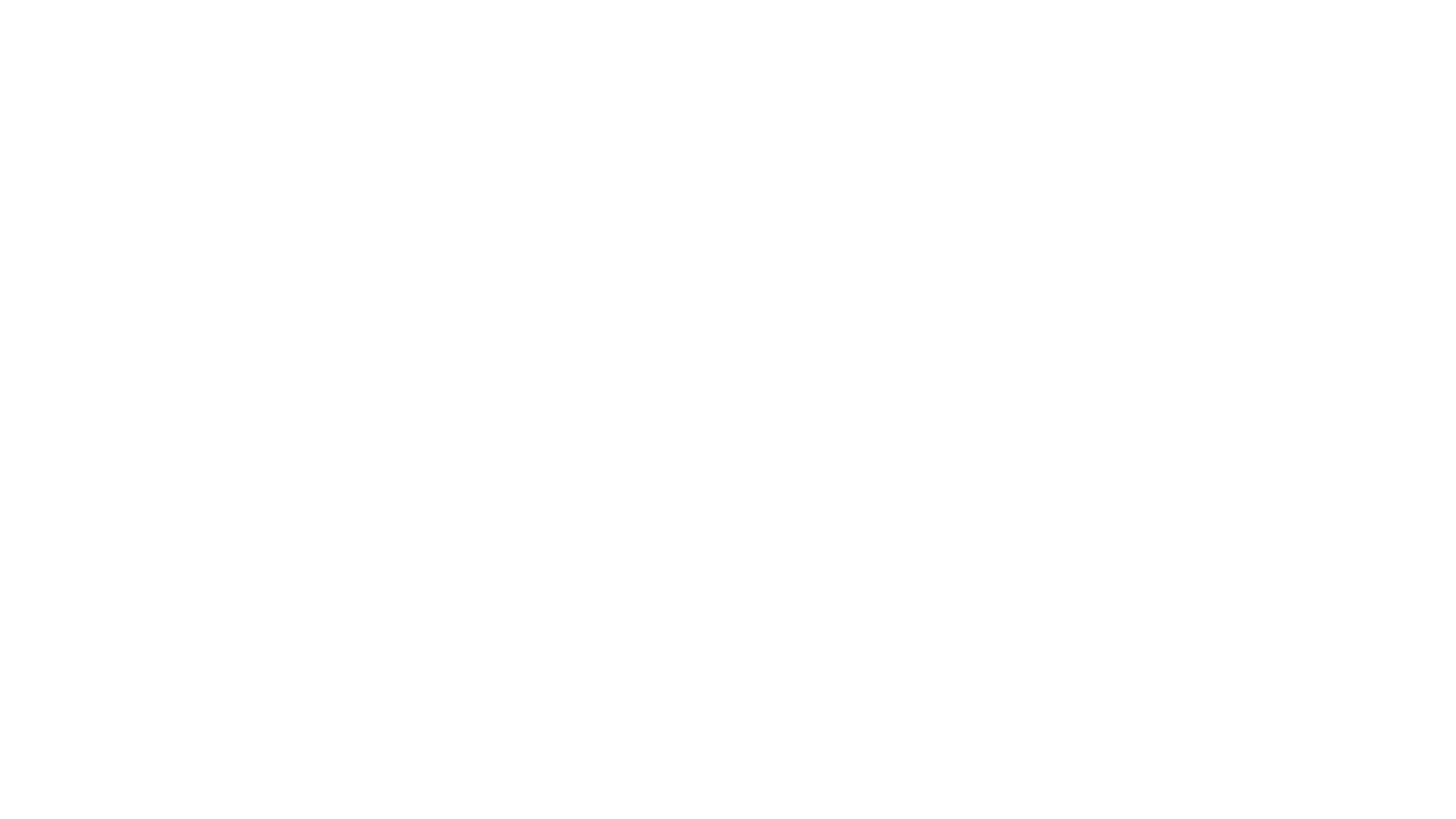
Interview: Doug Hines, CEO, Offshore Wind Power Systems of Texas
Talking exclusively to A Word About Wind, Hines told us why we should expect failures in the offshore floating wind market
- Floating offshore wind farms have major structural flaws, claims Hines
- He argues that project designers are overlooking some serious risks
- Structural problems will be more common than the industry realises, he says
Doug Hines is a man on a mission.
That mission is to raise awareness of what he sees as some serious flaws in the designs for floating offshore wind farms.
And the CEO of Offshore Wind Power Systems of Texas says that attention should be paid to the substructures of offshore floating wind farms in particular.
Talking exclusively to A Word About Wind, Hines told us why we should expect failures in the offshore floating wind market, the key issues project designers are overlooking, and why serious problems affecting floating wind projects could be more common than you think.
What should we learn from the experiences of the offshore oil and gas industry?
The wind industry’s 20 years of experience hammering monopiles and jackets into the seabed will do little to inform offshore wind farm designers in the development of floating foundations. They are entirely different systems. Indeed, the application of relatively static structures (monopiles and jackets) securely pinned to the seafloor in a dynamic environment (the sea) will not translate to the design of dynamic structures such as those used for high-center-of-gravity floating foundations.
What are the biggest challenges floating offshore wind faces?
Mooring lines have been a high-maintenance concern in the offshore floating oilfields for decades. A reliable mooring solution to the many challenges presented by the ocean has never been developed. That means you should expect failures and mitigate for them. Take the entire destruction of two separate floating solar power islands off the coast of Japan two weeks apart in September 2019, one near Ichihara City and the other near the Kyushu region. Neither of these storms set any records, one reaching average wind speeds of 41 m/s, and the other reaching an average of 40 m/s. In both cases, the root cause of the total destruction of these two floating systems was determined to be mooring system failure that occurred well within the design specification.
One of these platforms, the 13.7 MW Yamakura Dam array, was designed with 112 mooring lines and anchors on the north end, another 107 on the western side, 133 on the eastern side, and 68 on the southern edge. All 420 of the mooring systems on the platform, in addition to the ballast water held in each section of the structure to compensate for uplift from strong winds, did not constrain the array when the first mooring systems began to fail under dynamic storm loads.
While project designers often give consideration to the impact of large waves, is enough attention paid to the impact of troughs?
Troughs can form between waves where the maximum depth of the trough can be the negative equivalent to the maximum height of any wave. In other words, if the conditions are such that you can have a 20-meter-high wave, you can also have a 20-meter-deep trough.
Our team have worked with offshore wind farm developers for over 12 years, and have yet to hear from any developer who seriously considers the storm trough to be a significant challenge for the designed operating conditions of a floating wind turbine foundation. They give most of their design attention to extreme wave height, which makes sense if your experience is with static structures that are pile-driven into the seabed. For floaters, however, an extreme trough is an equally serious consideration.
What exactly are the issues posed by troughs?
For a conventional floating foundation, maximum waves can be adequately compensated for using dynamic ballasting in addition to tension provided by the mooring system. The foundation will ride through with the wave breaking against and over the structure, and significant uplift will be constrained by the mooring lines and ballast. But that’s not how it works with a storm trough.
When a significant trough appears beneath the structure, no amount of mooring line tension or ballast water will prevent the system from going into freefall, tilting and sliding down the side of the trough, bottoming out after a drop of 10 meters or more, and then rise again on its buoyancy where the sudden reapplication of tension from the mooring system will induce a jarring snap load into the structure. Looking at this from a wind turbine perspective, such a snap load can cause a mooring line to break and presents a significant risk of damage to the turbine’s main bearing on the main rotor shaft. Additionally, when a mooring line breaks under such tension, as they often do, the line can whip at a speed faster than sound and rip a hole right through the substructure.
What lessons can the floating offshore wind industry learn from the oil and gas sector?
Storm troughs and mooring line failures should not be considered a rare occurrence that might never happen during the operational life of a farm. These issues happen all the time. There are hundreds of professionally designed, formerly-floating oil rigs that litter the seafloor because of mooring line failures.
The offshore wind industry would do well to draw upon the vast number of experienced professional floating platform architects and operations engineers in the offshore floating oil and gas industry who know these risks and the appropriate mitigation strategies better than anyone who has only had experience with offshore wind’s static structures.